
Innisfree
How hundreds of unique millwork components and tiny details add up to one incredible shopping experience.
When Innisfree approached us about their flagship store on Lexington Avenue in Manhattan, we knew there was an opportunity to deliver a truly exceptional space. The design concept included a decorative scaffolding system that climbed the walls and worked across the ceiling. The challenge was to find a way to make all the millwork look as if it is hanging from the scaffolding – even when it isn’t.
What we did.
01.
Smart Engineering for a
Distinctive Design.
Rather than starting with the cantilevered concrete island, or the perforated metal ceiling panels or the hickory veneer casework, we focused first on the LED lights — all 400 of them, each with its own wires and drivers. We re-imagined the scaffolding as a single 300-piece wire chase and set to work programming holes and slots in each of the tubes for precision laser cutting.
We layered in additional details to support the cabinetry and lightboxes, overhead video monitors, and banks of custom faux folding doors with ribbed glass.
With the functional details laid out, we turned to the individual design elements, developing a kit of parts to standardize as many components as possible. A ribbon of silicone-edged lightboxes – instrumental in establishing a balanced, cohesive design vocabulary – gave us recurring details around which to engineer the custom hickory wall units beneath. Once the kit of components was tightly engineered, we moved into the execution phase.
02.
Pre-construction Planning
and Fabrication.
An early site survey helped us confirm overall dimensions. From there, we worked with the client’s general contractor to develop the attachment plans for the custom ceiling grid tiles, the scaffolding array that climbs up the side of the mezzanine staircase, and the structural elements that hold the center island in place.
Alongside the client’s architect, we fine-tuned the concrete and hickory finishes and worked out bespoke details including custom drawer pulls and ribbed glass specs – all while sprinting through the approval drawing process. At the same time, we put trusted sub-contractors to work on key elements; ordered raw materials from across the US, Canada, and Asia; programmed the CNC routers and computerized doweling centers; and set to work building the millwork.
03.
Delivery, Installation,
and Onsite Coordination.
Because of the sheer scale of the millwork package, and because New York City street rules limit truck access, we delivered the project with 12 straight trucks — all on an overnight basis to comply with parking restrictions in midtown Manhattan. Our installation team tackled the scaffolding and ceiling grid first, then layered in the wood cabinetry, lightboxes, faux folding doors, and, ultimately, the center concrete table.
Intense cooperation with the site electrician, plumber, audio/visual vendor, merchandisers, and even their botanist (whose scope was to water plants directly above our multitude of electrical wires!) delivered the immersive customer experience that is so crucial to the client’s design vision.
This project won several prestigious “Store of the Year” awards across the retail design sector. For us, Innisfree stands as the end-product of months of hard work and the upshot of a process rooted in innovation, resourcefulness, and partnership.













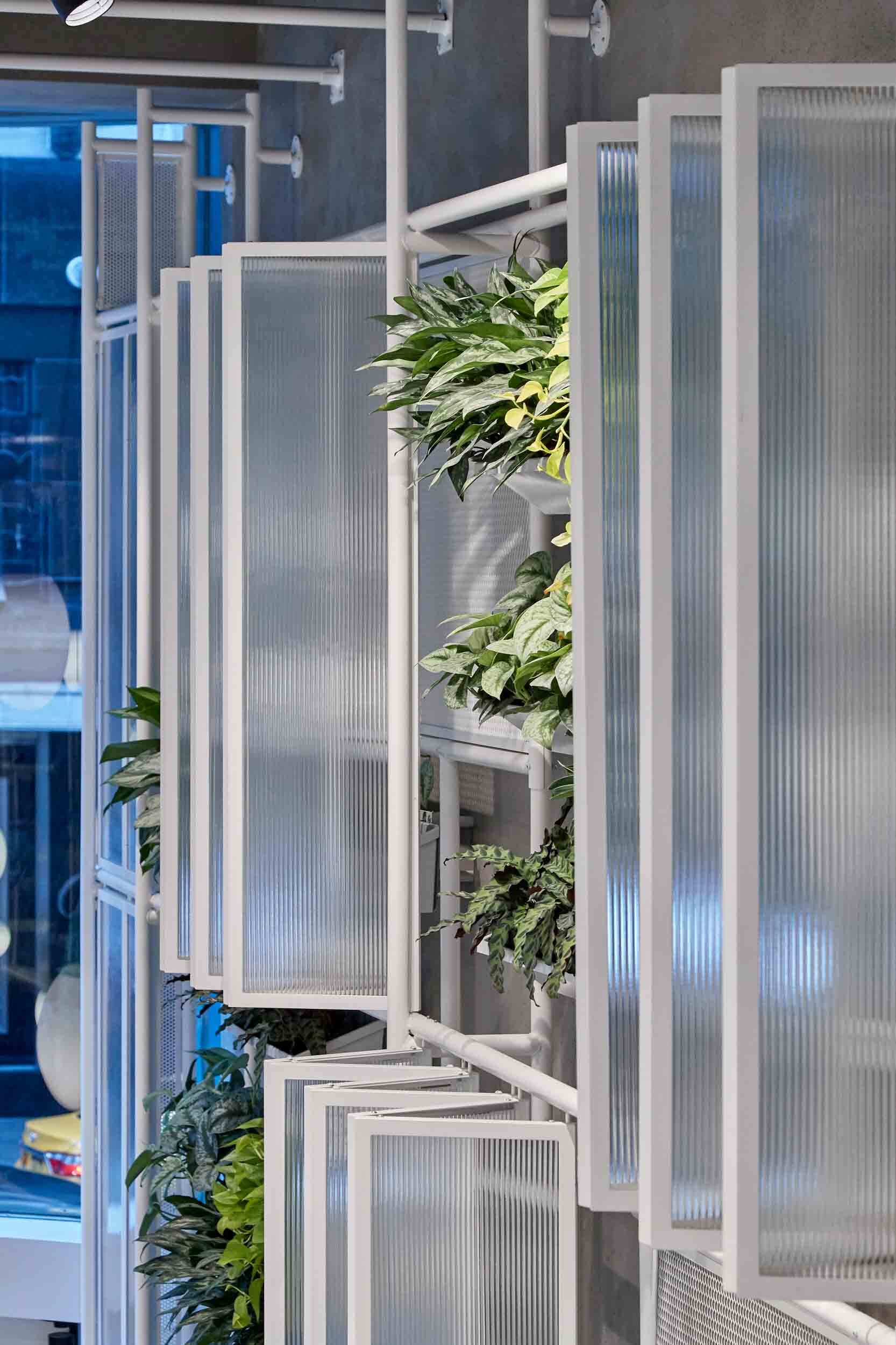
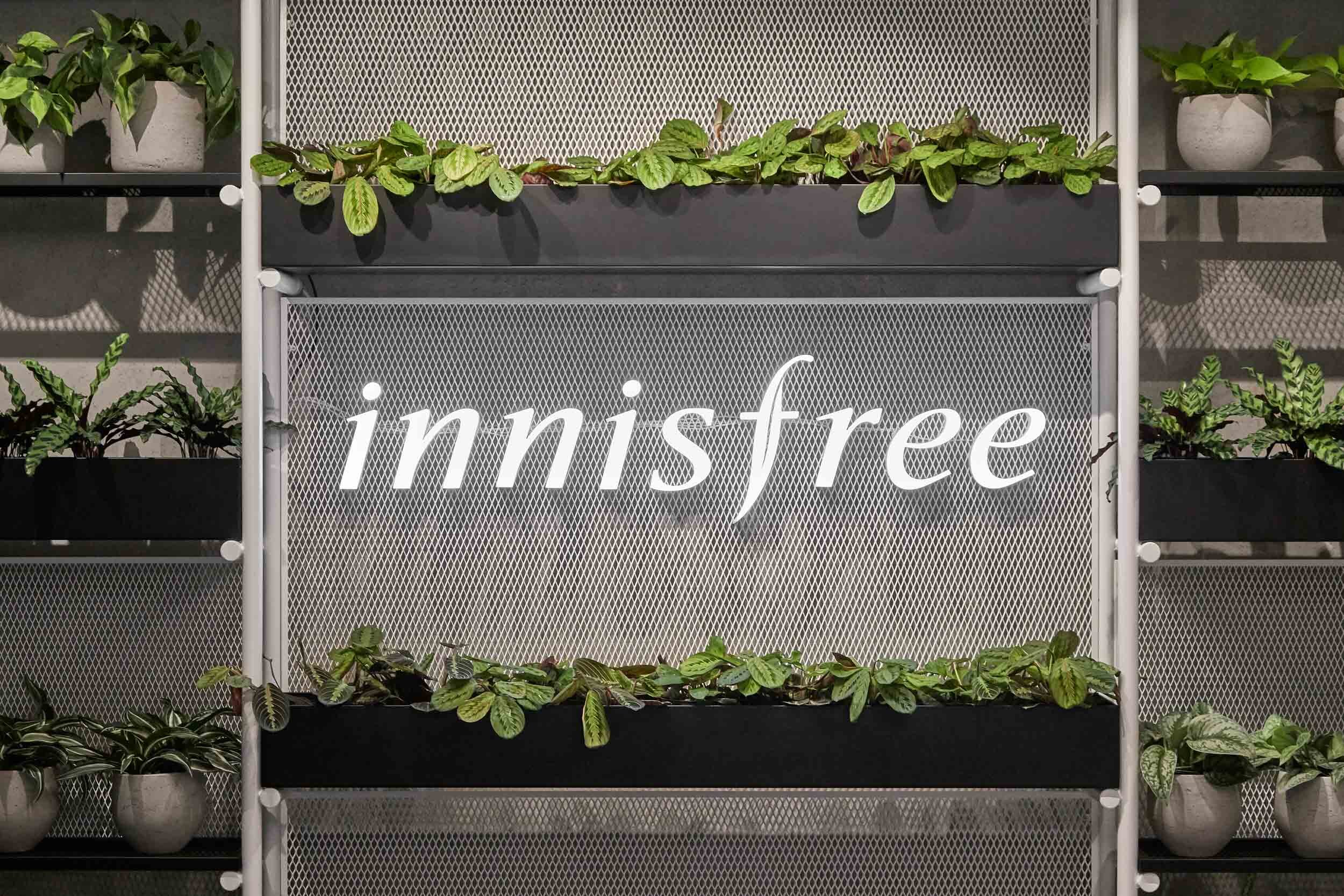


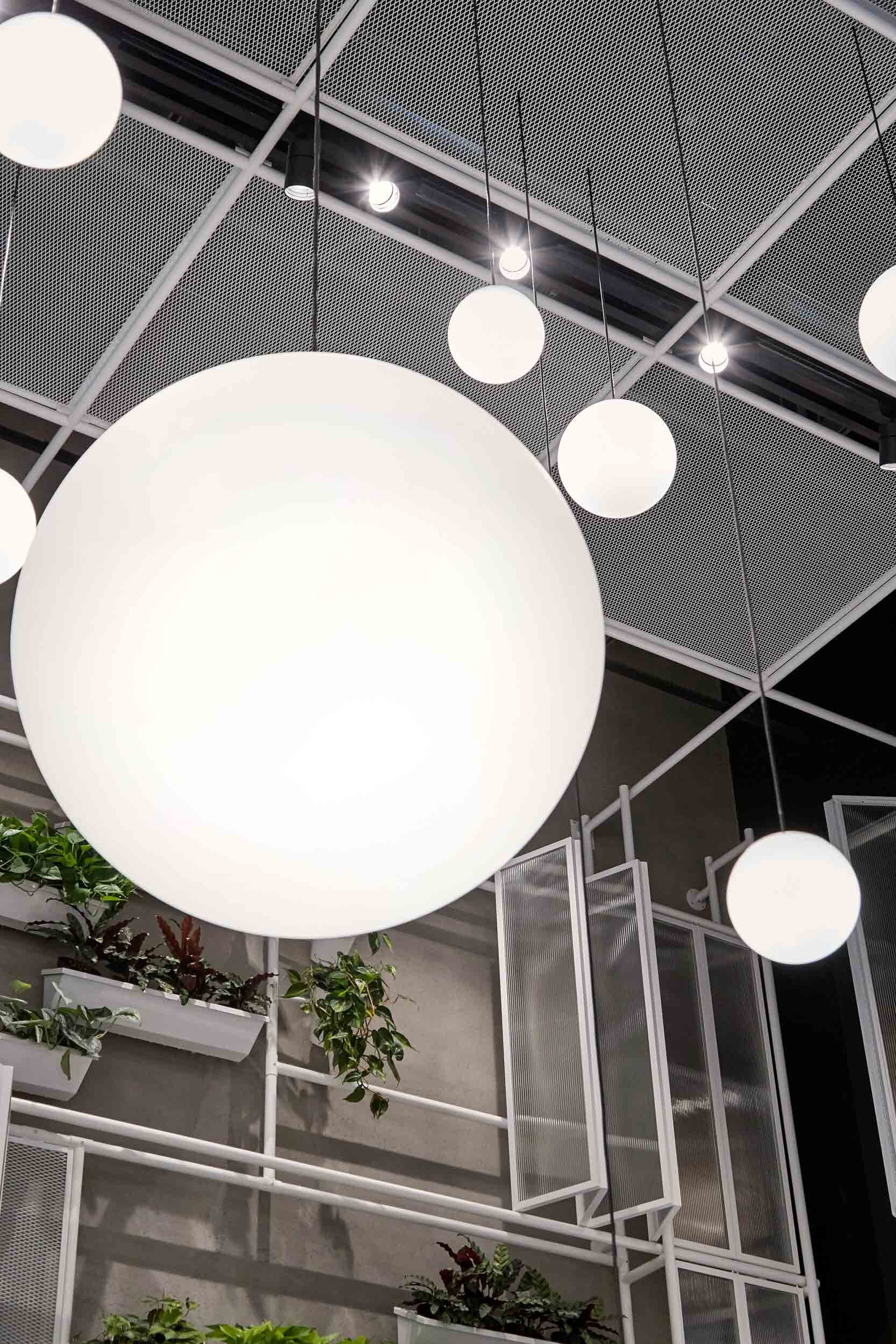

